Material Handling and Distribution
Name
Institution
Material Handling代写 Physical distribution system involves the activities that are associated with the supply of finished product at···
The physical distribution system
Physical distribution system involves the activities that are associated with the supply of finished product at every step beginning with the production and ending with the consumer. The distribution process should be efficient to ensure lower costs and timely delivery of the products to the customers. It involves functions such as inventory control, processing of various orders, transportation, logistics and also material packaging (Widup, 2014). These processes should also work in harmony to ensure proper coordination of distribution activities.
Elements of the material control system Material Handling代写
Material control is the precise control of purchases, storage and consumption materials. The primary purpose of material control is to ensure efficient and uninterrupted production of output and avoid obsolescence of material by maintaining a regular and timely supply of materials and avoid overstocking. Material control also reduces the cost of production and increases the profitability of a company (Frank, 2009). It includes how the company can control its raw materials, work-in-progress and finished products.
Inventory control involves the use of policies and systems like purchasing, shipping, receiving, storing and reorder levels. Proper coordination and corporation among the various departments dealing with the receiving, testing, storing, production planning and accounting are some of the main elements of material control that should be focused on. Moreover, there should be the establishment of a centralized purchasing department. An essential element of the material control system is classification of materials and availability of an effective system of internal checks.
Employ a physical inventory and storage system with the required inventory levels Material Handling代写
The company has a system where inventories are not supposed to overstay in the warehouse. To achieve this, it employes the economic order quantity and safe stocks. The policy ensures holding costs are low and hence increase profit margins.
Physical inventory | Storage system | Required inventory levels |
It is the process of physically counting the inventory levels | Warehouse | At 1per unit 300
At 2 per unit 600 At 0.5 per unit 150
|
Prepare a demand ordering system Material Handling代写
The period in which the order is taken | Amount of order |
1st week
2nd week 3rd week 4th week 5th week 6th week |
100
100 100 200 200 200 |
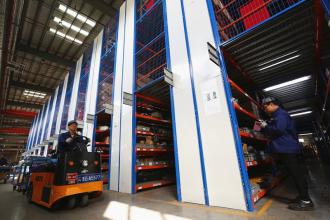
Management Resource planning
Resource planning is a key aspect in supply chain management. Resource planning is a specific area in project management that deals with gathering and making use of resources required to deliver the product/services. The plan starts with the production required at the end of each week, reorder level, and lead time for each product.
3 weeks earlier | 2 weeks earlier | 1 week earlier | 1 | 2 | 3 | 4 | 5 | 6 | |
Production Required by the end of the week | 300 | 200 | 100 | 100 | 100 | 100 | 200 | 200 | 200 |
Total As needed at 1 per unit | 300 | 200 | 100 | 100 | 100 | 100 | 200 | 200 | 200 |
When must As be ordered, and how many: 1 week lead time | At the beginning of the 6th week.
100 units |
||||||||
Total Bs needed at 2/unit | 600 | 400 | 200 | 200 | 200 | 200 | 600 | 600 | 600 |
When must Bs be ordered, and how many: 2 week lead time |
|
At the beginning of the first week
400 units should be ordered |
|||||||
Total Cs needed at 0.5/unit | 150 | 100 | 50 | 50 | 50 | 50 | 100 | 100 | 100 |
When must Cs be ordered, and how many: 3 week lead time |
At the beginning of the 2nd week. 150 units should be ordered |
Factors to consider when determining an ideal warehouse location Material Handling代写
Because the insulator coolers are bulky products, the first factor to consider will be the proximity to carrier facilities. This will ease the process of delivering the products to the consumer (Widup, 2014). A second factor to consider will be the proximity to the consumers. For example, the warehouse should be located in southern states and southwest during winter and should be located in the east coast during the summer months. A third factor to be considered will be the availability of workforce to operate the warehouse. Notably, warehouse location determines the cost of distribution to the customers as well as transportation to the warehouse for storage and holding costs.
Describe the pros and cons of setting up your trucking fleet to take a product from your factory to the new warehouse vs. using common carriers Material Handling代写
The pros of setting up your trucking fleet are the convenience of having your own transportation readily available, you will have dependable and reliable transportation at your fingertips because you control the services, it will ultimately cut costs and it will reduce time constraints that come with using common couriers (Widup, 2014) and it allows for flexibility. The cons of setting up a trucking fleet are the additional costs derived from hiring drivers, and also maintenance costs and high insurance costs associated with this short-term expense, as opposed to using common carriers.
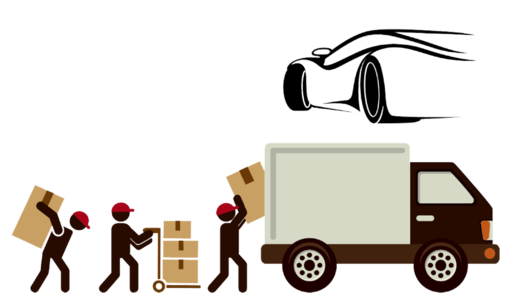
Given the high dollar value of your inventory, how can you ensure the accuracy of both purchased raw material inventory in your factory as well as the finished product itself in your factory and at the new warehouse
This can be achieved by the preparation of a final management resource plan. Inventory accuracy is one of the major performance factors in any distribution center. There steps which can be followed including maintaining well-organized warehouse and establishing good inventory naming and labeling practices. Besides, the manager can define and follow efficient storage process and cycle counting. Also important in maintaining inventory accuracy is the limit and tract access to inventory and use of technology in inventory management systems.
How will planning for equipment capacity needs to be done if you use a forecast based system versus a demand management system-based system
When using a forecast-based system planning of equipment will be based on credible forecasts and are funded and implemented before the disaster strikes. When using the demand management system, the planning of equipment will be done based on forecast needed to manage the demand of products and services.
MRP – Template for Unit 4 Individual Project (Key Assignment) Material Handling代写
Manufacturing Resource Planning is essential in planning for all resources of a manufacturing company. The MRP addresses the operational, financial, and capacity planning of the company. The main advantage of MRP is timely availability of the materials required for production. The planning ensures little if any excess inventories in the warehouse and ensure timely delivery of the finished goods to the consumers. Besides, the MRP ensure optimal use of the manufacturing resources which result to overall reduction in capital use. However, MRP may be affected by data accuracy which may affect planning for resources.
Below is the MRP for the company starting with the sales forecast which is compared with the amount of the inventory needed at the end of the period. The opening inventory is compared with the demand to determine the production needed. The closing inventory reflect the remaining inventory after the sales. As such, the closing inventory become the following period opening inventory and determine the production levels.
Month | -2 | -1 | 1 | 2 | 3 | 4 | 5 | 6 |
Sales forecast by month | 100 | 200 | 1,100 | 1,100 | 1,150 | 1,200 | 1,200 | 1,300 |
Finished goods Inventory Required by the end of the month: | 800 | 900 | 950 | 1050 | 1,100 | 1,200 | ||
Beginning inventory | 300 | 200 | 200 | 150 | 100 | 100 | ||
Sales made | 900 | 1,000 | 1,050 | 1,150 | 1,000 | 1,200 | ||
Ending Inventory | 200 | 100 | 100 | 50 | 100 | |||
Production needed | 900 | 1,100 | 1,100 | 1050 | 1,00 | 1,100 | ||
How many and when must Be ordered at 2 per finished product; assume no safety stock of Bs are desired | 200 | 400 | 2,000 | 2,200 | 2,300 | 2,400 | 2,400 | 2,600 |
References Material Handling代写
Frank B. Watts (2009). Bill of materials. Engineering Documentation Control Handbook.
White, J. R., & Widup, R. (2014). Factors to Consider When Determining Maintenance Intervals. IEEE Transactions on Industry Applications, 50(1), 188-194. doi:10.1109/tia.2013.2288229
更多其他:电子商务代写 管理学代写 统计代写 考古学代写 计算机科学代写 语言学代写 金融学代写 音乐学代写 保险学代写 时尚设计代写 电影代写 组织行为 项目管理代写 It代写